Photo History of Sudbury's Stressed Environment
Background
It is a little known fact that the original stress to the Sudbury environment and more specifically to its landscape was clear cut logging.
The area was covered in mature white pine forests which grew tall and straight; dooming them to destruction.
A prime drive behind the logging was the need for lumber during the rebuild of the city of Chicago after the Great Fire of the late 1800's.
The clear cut logging practices of the time left behind large amounts of "slash" ie wood leftovers such as leaves, branches, bark, small trees destroyed by larger trees during their felling, and scrub trees unsuited for lumber.
Once this scrub dried, the area became a tinderbox and many many fires of natural and human causes raged through the area.
Between the pressure of clear cutting and the fires, the thin Canadian Shield soils became extremely vulnerable to erosion as the vegetation which held it together began to die.
The additional pressure of early mining and smelting practices, with both an acute and chronic effect, proved too great for the remaining vegetation.
The soil structure collapsed, eroded away, and the area became famous for denuded hills and barren clay mud flats in the interlying valleys.
Logging
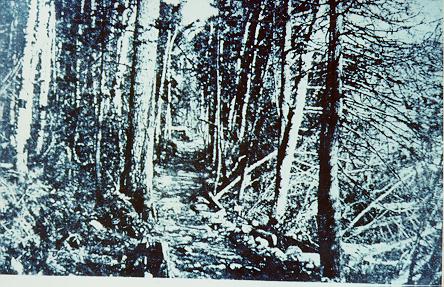
The image above is of the original tote road through the area to service the construction of the Canadian Pacific Railroad in the late 1800's.
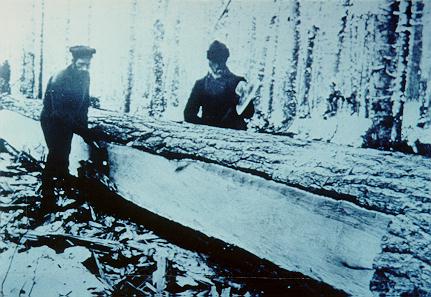
The loggers in this image are hard at work on one of the large white pines from the area.
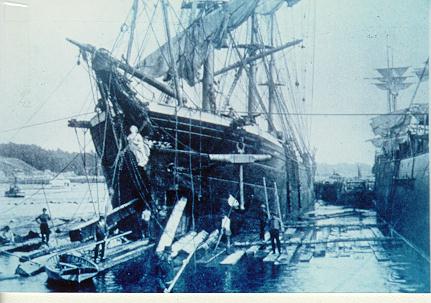
The ship image is typical of the fleet of front loading log/lumber carriers used on the Great Lakes. This one is taken at Spanish Harbour.
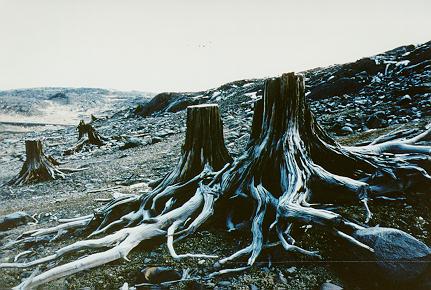
The outcome of clear cutting is all too evident. Note the shallow soil depths in which the great trees grew.
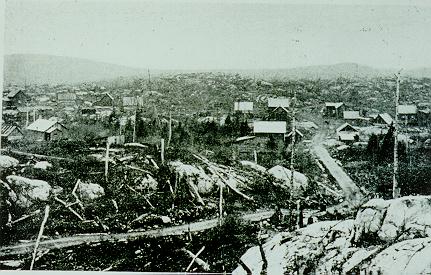
An early image of the area taken after the loggers were finished but before any mining/smelting activity started. The environmental stress on the landcape is clearly evident.
A quote from the journal of a Canadian Pacific Railroad surveyor in 1883.
Mining
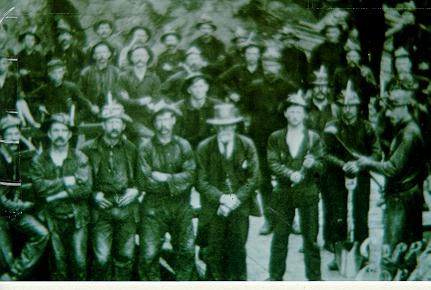
A typical crew of miners with candles on their hats for light. Lucky miners got to wear acetylene open flame lights. Note the lack of personal protective equipment such as masks, gloves, and workboots.
Roast Yard Technology

In the early years of the century (up to 1929) the ore was pretreated prior to refining out of the country in either the USA or the UK.
The major portion of the sulphur in the ore was removed by in "open bed roast yards".
Remaining and stunted regrowth logs were piled about 1 to 2 m deep and overlain with 5 m piles of ore. These were then set on fire.
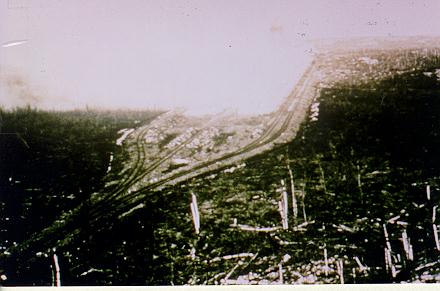
The fires smouldered anywhere from three to six months releasing flora-toxic ground level concentrations of sulphur dioxide and contaminating the soils beneath with acid and heavy metals.
There was a townsite for the workers located a kilometer away from this particular roastyard called "ODonnell". It has a one room schoolhouse in which the teacher was allowed to dismiss the students when the children couldn't see the blackboard due to the offgases from the roastyard.
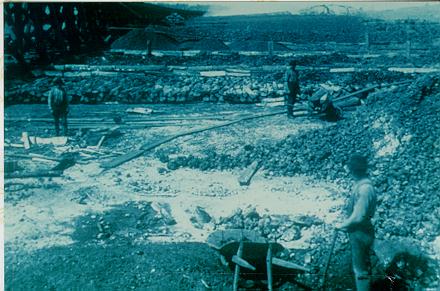
Roastyard workers hand remove the partially smelted ore. Note that they did this while part of the heap was still on fire as shown by the white plume at the top of the photo.
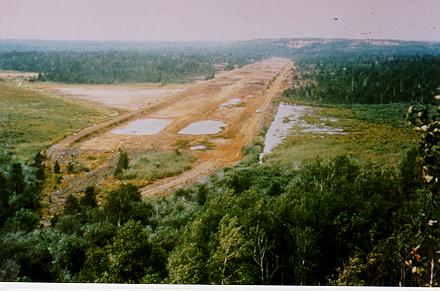
The environmental legacy of roastyard technology is clearly evident in this image taken exactly 60 years after the operation ceased in 1929. This particular roastyard is about 2 kilometers long and shows up on satelitte photos.
Smelter Technology
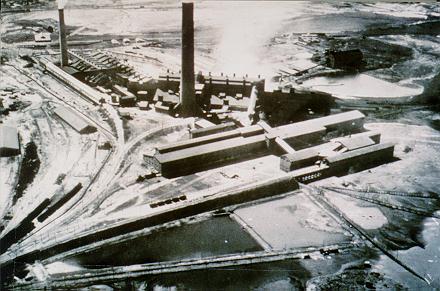
In 1929 the Copper Cliff Smelter was built. There were earlier smelters on site which used blast furnace technology. The 1929 smelter saw the first use of reverberatory furnaces
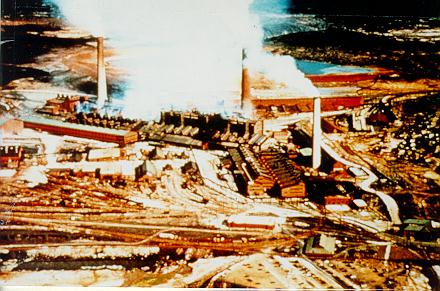
The infamous heyday of sulphur dioxide emissions from the Sudbury operations; 1965 at over 2,500,000 tonnes released.
Fugitive release of gas and particulate from the roofs created a zone of severely stressed land around the smelter. A similar effect occured arond the nearby Coniston smelter and the Falconbridge LImited smelter.
The blackened hills in the background attest to the intensity. The black colour is a surface layer about 2 to 3 mm thick on what is naturally a beige coloured rock. The acidic emissions leached the light coloured "basic" components of the rock, leaving behind the dark "acidic" components of the rock.
The stack gases were released at about 167 m, creating a well documented ovoid environmental footprint around the facility aligned along the predominant southwest to northeast wind direciton .
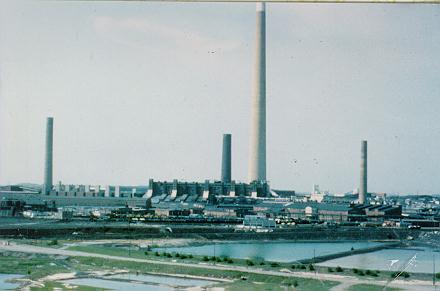
The world famous (infamous?) 381 m Superstack which came on line in 1972 and has come to symbolize atmospheric environmental impact.
It greatly improved the local environment and allowed for a natural and anthroprogenic regreening of the area.
The theory behind building it was that by the time that the offgas reach ground level, it would be so dilute as to not have an effect. (Dilution-solution-pollution!)
Modelling knowledge at the time could not incorporate the complex terrain which had been created in the area.
The blackened hills had become "black body" heat islands between which lay cool myriad lakes.
This creates ideal conditions for setup of strong convective cells in the atmosphere. The power and size of these cells are such that they reach up to stack height and pull the plume down to the ground.
Localised short duration fumigations occur which are controlled by cutting back or shutting down the smelter.
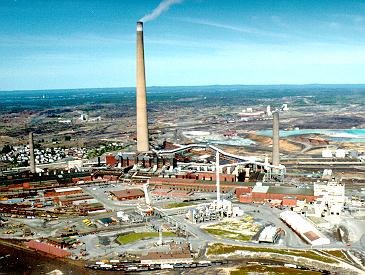
The smelter underwent a major on-the-fly rebuild and process technology change in the period 1990 to 1994. Once the project was completed, a complete reversal in emission rates had been effected.
In 1972 the facility released 90% of the ore's sulphur content. In 1994 the facility captured >90% of the sulphur in ore.
The effect on local vegetation is proven by the green of the grass in the foreground and the recovering forest in the background.
The facility is now at a tradeoff position. The sulphur in the feed is also the fuel for the process. Little or no fossil fuel is used in the new process. Additional removal of sulpur units prior to smelting would result in the need to use fossil fuel.
One of the driving forces behind the emission reductions was reducing acid rain. Fossil fuel combustion generates NOx and CO2 which would generate acid rain.
Capture of additional process gases for treatment in the onsite acid plant (small white stack and buildings in foreground) could bring the sulphur captrure percentage into the high ninties, a globally excellent performance.
It is comforting to note that the facility has fallen out of the top ten emitters of SO2 in North America after decades of being the No 1 global point source. (That honour? now belongs to the Russian smelter in Norilsk, Siberia)
Created by Dan Bouillon 010721
Revised 010721